DMAIC RCA: A Proven Approach to Reliability
What is DMAIC RCA?
DMAIC, pronounced “duh-may-ik," is a data-driven approach to problem-solving designed to identify and improve existing process inefficiencies with unknown causes.
As one of the most important tools in any continuous improvement toolbox, this five-phase strategy - Define, Measure, Analyze, Improve and Control (DMAIC) - acts as the foundation for any process improvement project. Most often associated with Six Sigma or Lean methodologies, DMAIC is also used by those who don’t subscribe to any methodology but rather share a common goal of improving operations and becoming more efficient.
With proper implementation, the DMAIC process provides an effective problem-solving framework to standardize root cause thinking, reduce variability, and ensure world-class Root Cause Analysis (RCA) results.
DMAIC RCA has 5 key steps:
Define:
Define the problem against various areas affected such as; HSE, Reliability, Quality, Production, Vehicle, etc. Get to grips with exactly what the current state is and what the intended improvement outcomes should be.
- Identify opportunities with high potential for improvement
- Estimate the impact the project will have
- Provide an overview of an entire process
- Record incident details
- Define data collection and measurement requirements for evidence
Measure:
Measure the process so you can see what the impact of the problem is. Define what you’re going to measure, so you can understand the problem in greater detail. Map the process to determine the exact events leading up to the incident and start sorting through the details to collect and organize the data for analysis.
- Identify input, processes, and output indicators
- Outline the Failure Modes and Effects Analysis (FMEA)
- Gather, collect, and examine evidence with current state data (asset health readings, maintenance records, photos, interviews, personal accounts, etc.)
- Establish the baseline process "as is" and define the goals of the investigation
Analyze:
Analyze the process to understand the root cause(s) and the reasons for defects. Investigate the data collected from the measure phase into fact-driven evidence to determine potential causes. Visually display and identify the root cause through RCA tools and suggest corrective actions.
- Complete a root cause analysis (Five Whys, Fishbone/Ishikawa, Cause Map)
- Determine an incident’s risk using a Risk Matrix and review any mitigations against its Failure Mode libraries
- Complete an FMEA for identifying possible equipment, service, and process failures
- Develop an improvement plan with recommended actions to eliminate or mitigate the effect of the problem
Improve:
Improve the process by eliminating the root causes. Analyze and validate the suggested actions from the Analyze phase and develop an implementation plan to gain approval and ensure effective change management.
- Gather potential solutions or generate new ones with facts uncovered from the analysis
- Weigh each solution to determine viability and effectiveness using process maps or PDAC methods
- Outline a pilot/test solution and implementation plan
- Make a final decision and implement the solution
Control:
Control future performance of the process by standardizing the new way of working. Track the implementation and effects to prove the recurring problem has been eliminated or indicate further actions/analysis is needed. Create an A3 report to identify performance trends and share learnings.
- Create a Monitoring Plan to track implementations and verify failure reductions
- Develop and initiate a Response Plan if improvements start to decline
- Document the new work standard
- Integrate and communicate the lessons learned with A3 Reporting
- Continuously improve the process
Summing It All Up
DMAIC can be quick and easy for simple problems with clear root causes, or it can involve many improvement tools and cross-functional collaboration for more difficult challenges. In either case, it requires discipline and attention to detail, two very important elements of continuous improvement.
The simple, yet highly structured DMAIC process provides organizations with a well-defined and consistent approach to problem-solving that supports productivity, collaboration, and a reliability-focused culture.
What's Next?
Now that you have a clear picture of a DMAIC RCA process. Let's talk about adopting DMAIC RCA within your organization.
As new technologies continually make their way into the business landscape, the race to the bottom line is more competitive than ever. As such, more and more organizations are turning to DMAIC using improvement technologies to gain and maintain a competitive edge.
With efficiency at its core, implementing a DMAIC strategy should never be costly, timely, or challenging. Investigation Optimizer™ guides you through each step of a Lean Six Sigma DMAIC process as a simple, reliable RCA and continuous improvement software. Entire organizations can collaborate with ease and share lessons learned to quickly and confidently solve problems, reduce risk, and continuously improve performance.
Topics: Article, Investigation Management
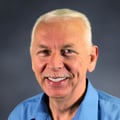
Posted by
Larry Olson | CMRP, CRL, CAMA
CEO, Nexus Global | Larry is one of the leading global Shutdown/Turnaround, Asset Integrity, and Maintenance strategists. With over 30+ years of business & maintenance experience, he has carried out a variety of roles from Project Manager, Change Management Specialist to Director of Reliability & Integrity Assurance Excellence.