Removing Bad Habits
Most professionals have the good fortune of working for really fantastic leaders, but also the misfortune of working with a few ineffective leaders. Truly inspiring leaders lead by example, possess a great deal of empathy for others, never get overly excited and understand the complexities of developing a sustainable proactive maintenance organization. “Complexities” is the optimum word here. There are so many attributes in establishing and maintaining proactive industrial maintenance that it’s often difficult to put all the pieces of the puzzle together and know where to focus one’s energy.
To many, the most important aspects of any organization are the people within it. There are key levers in achieving world-class proactive maintenance with a special focus on the human element, particularly the removal of bad habits while establishing productive habits.
In Charles Duhigg's book, The Power of Habits, the psychology of habits is outlined in three distinct stages:
- Cue: a signal to the brain on which habit to follow
- Routine: the script to follow or action taken
- Reward: the satisfaction and expected outcomes
Habits, as Duhigg explains, are automatically established by the human brain to manage routine tasks to conserve brain power. Think about your morning routine. It’s typically the same sequence day in and day out; it’s our brain’s way of organizing routine tasks, which saves brain capacity for more pressing thoughts like what to get your wife for her birthday. Have you ever driven home from work, got lost in thought, and then found yourself three or four miles further down the road than you realized?
That’s the basal ganglia taking over – a place in the brain where habits are formed and stored.1 In our lifetime, about 57 percent of our waking hours as an adult are spent working, which leads to plenty of opportunity for establishing routine tasks and bad habits.
Breaking away from reactive maintenance is all about eliminating bad habits. By understanding the different phases of habits (cue, routine and reward), we begin to understand how to modify our organization’s behaviors and promote proactive maintenance. Here is an example:
The Cue: An emergency happens, such as the production line is going down.
The Routine: The maintenance team springs into action and fixes the problem.
The Reward: The team gets an “attaboy” all around, huge thanks for a job well done and the distinction of being an effective and important member of the team.
No problem, right? Why would you want to change that?
The issue occurs when reactive maintenance becomes a habitual part of your organizational culture. To be successful at implementing proactive maintenance, more constructive habits must be put into place and promoted.
Most work is routine in nature. It’s within these routines that we’ll find the secret sauce to breaking the cycle of reactive maintenance. In order to effectively move an organization into a proactive state, we must understand what is really holding our team back.
Let’s examine some bad habits that promote reactive maintenance:
LEADERSHIP
Each week, there are reminders of failed leadership: industrial accidents, retail conglomerates imploding, missteps by global political leaders. In these cases, leadership loses focus on the importance of serving the people associated to their organization, whether they are customers, employees or stakeholders. While it is important for leaders not to be excitable individuals, they must have a passion and empathy for the human element. Leaders should understand how each person fits into their organization, not just understand how the work moves through the process. Leaders must also learn to appreciate the complexities of the individuals performing the value added task.
Bad Habit #1: Accepting the Normalization of Deviance
As a work culture, accepting reactive maintenance firefighting is accepting a “Normalization of Deviance,” where people within the organization become so accustomed to a deviant behavior that they don’t consider it as deviant despite the fact that they far exceed their own rules for the elementary safety.2 We’ve seen many times where the institutionalization of Normalization of Deviance leads to tragic results, such as in the 2005 BP Texas City explosion and NASA’s 1986 Challenger explosion. The bad habit of accepting a certain level of risk equates to exposing your team to predictable failures. To this end, reactive maintenance is more dangerous to perform because of the lack of planning that, by nature, is designed to mitigate hazardous events from happening in the first place.
Bad Habit #2: Not Leveraging Big Data to Drive Improvements and Gain Process Visibility
Asset health dashboards and Key Performance Indicators (KPIs) are a manager’s window into the world of their maintenance organization, allowing them to visually appreciate the complexities of the individuals performing their value added task. By leveraging technology, in particular an asset health dashboard, managers can monitor the health of not only their equipment, but their processes as well. However, when it comes to KPIs, many organizations have a bad habit of using too many KPIs, making goals ambiguous and weakening organizational focus. The key is to start out with a few fundamental KPIs and process indicators. After your team gains some confidence, move on to more granular KPIs while aligning targets to business goals.
Here is an example of a few KPIs and process indicators to get your team started:
KPI | Process Indicators |
---|---|
% PM completion rate (monthly) | Initiated work order to approved for planning |
% Schedule completion (weekly) | Planning to ready for scheduling |
% Unplanned downtime due to maintenance (monthly) | Scheduled |
% PdM/PM to corrective maintenance (monthly) | Job technically completed |
Bad Habit #3: Allowing Processes to Be Ambiguous, Thus Enabling Poor Performers
Leaders sometimes don’t hold people to the same standard because it’s too difficult of a task to manage. In order to hold everyone to the same standard, organizations need to have clear roles and responsibilities that outline individual deliverables. I have been on consulting engagements when an interviewee has remarked, “The boss always piles the work on me because he knows I will get it done. This other guy is incompetent, but they keep him around anyways.”
Disciplining people is never a fun prospect, but the hard-working folks who do what is expected of them deserve leadership. There is no faster way to kill your proactive maintenance program then to have people in your organization skating through work when others are expected to pick up their slack. Build your processes by outlining expectations, roles and responsibilities.
Documentation and communication is important to a successful outcome, and a consistent message across all organization levels is imperative.
ORGANIZATION
Bad Habit #4: Not Being Confident Enough in Your Own Abilities to Let Others Grow
Talent, the ability to adapt and a clear understanding of expectations are important levers to any effective organization. Adaptability requires having the right tools available and a workforce that feels empowered to affect positive change in order to meet both short and long-term goals. As Jack Welch once said, “Before you are a leader, success is all about growing yourself. When you become a leader, success is all about growing others.” It’s wise to never give anyone responsibility without giving them some authority as well. Leaders need to let go of responsibility and let their direct reports have the opportunity to earn their wings.
Bad Habit #5: Not Growing Talent up Through the Organization
Our profession is facing a time where experienced and senior staff are reaching the age of retirement. Roles within organizations that are vital to the day-to-day execution of asset integrity are typically senior maintenance technicians who, over time, have progressed into management roles. These roles include maintenance superintendents, supervisors, schedulers and planners. In the past, unions played a key role in supporting training by promoting and establishing apprentice programs. These programs mitigated critical loss of talent and technical knowledge while also strengthening union membership. Apprenticeship programs have fallen out of favor and currently only 12 percent of American labor is unionized – a 20 percent decline over the last decade.3
Making matters worse, U.S. apprenticeship programs have shrunk by 36 percent since 1998, and enrollments have dropped by 16 percent since a peak in 2003.4 Mentor your team and develop a strategy for retaining talent and senior knowledge. Work with human resources to identify technicians’ competency and cultivate their talents to ensure a fully functioning and well-trained team.
Bad Habit #6: Poor Structure of Processes
Maintenance organizations should focus on instituting structured meeting cadence and good reporting habits to support proactive initiatives. The methodology for forming and managing a sustainable maintenance organization is called a Management Control and Reporting System (MCRS). MCRS is a closed-loop system, comprising of information, documents and meetings that are used to deliver quantifiable business performance improvements to:
- Reinforce essential behaviors, e.g. planning and problem solving
- Enable short-interval control of critical processes and activities
- Provide accurate and timely management information to make decisions
Bad habits typically associated to MCRS are poor meeting discipline, structure, and cadence. How many times have you sat in a meeting when an e-mail or phone call would have accomplished the same end result? I was invited to sit in on a colleague’s meeting with one of his clients and was amazed to find how poorly the manager ran the meeting. Turns out the manager held a meeting once a week and worked down his own personal action items with a room full of his direct reports chiming in from time-to-time to verify completion. This may lead to the perception that the direct reports’ time is not as valuable to the manager or the organization.
All meetings should have agendas and actionable outputs; otherwise it is simply a social event. Reinforce proper meeting cadence by utilizing meeting audits. Meeting audits allow organizations to coach their team on holding effective, organized meetings that maximize attendees’ available time.
Bad Habit #7: Not Quantifying the Maintenance Process
Typically, maintenance costs comprise 20 to 30 percent of total operating expense costs in terms of driving efficiency savings. Equating equipment reliability directly to throughput is vital for management’s understanding of the real value of maintenance. When developing organizational goals, use milestones and communicate savings in real dollars. Celebrate your wins and infuse your team with a “can-do” attitude.
EQUIPMENT OWNERSHIP
Bad Habit #8: Not Promoting Equipment Ownership
The importance of equipment ownership cannot be understated. Have you ever witnessed the hand-off between production and maintenance? Production has locked out the equipment and it’s now on maintenance to do their job. This leads to ownership not requiring production to assist and/or participate in the maintenance process. Once they hand the equipment over, it’s no longer production’s problem. An “I will get the equipment back when I get it back” attitude sets in. Equipment ownership is everyone’s problem because it’s about asset integrity, meaning proper operation and maintenance of the equipment. Augment equipment ownership by performing equipment availability audits. Equipment availability audits ensure no outstanding anomalies are being overlooked by operators in their daily rounds. Have operators enter work orders and get them involved in capital expenditure projects in the selection and improvement of assets.
EQUIPMENT HISTORY
Bad Habit #9: Not Understanding the Importance of History
Work history is an interim control of the continuous improvement loop in maintaining asset integrity. The bad habit here is not following up with technicians to ensure they provide sufficient history.
Maintenance supervisors must get in the habit of reviewing job history daily to ensure they are promoting the right behaviors. Reinforce the good habits by initiating the award of a “job well done” to the technicians. That being said, if the history is insufficient, then the bad behavior must be corrected. History is also vital to the reliability centered maintenance (RCM) process and plays a key role in PM optimization (PMO). Be sure your team is leveraging your computerized maintenance management system (CMMS) system to take advantage on RCM functions.
PLANNING
Bad Habit #10: Planning from Behind the Desk
Some think when it comes to planning, maintenance planners are so good they don’t need to walk down jobs. This is false. Not walking down jobs is a bad habit because planners cannot plan the job from their desk. In my own experience, I’ve witnessed experienced planners who think they know a job inside and out so they don’t bother to walk down a job. When it comes time to execute the work, they find they missed something. Missing something in a job plan can get people hurt.
Every time we walk down a job we should utilize a job walk down sheet, much like a preflight checklist. Preflight checklists came about when an experienced air force test pilot forgot a simple step before his take off and almost got himself killed. The job walk down checklist helps us reinforce good habits by verifying sequential steps and removing any question of omission, which are vital when our plan could possibly impact safety or production. Reinforce job walk habits by using the job feedback form and getting feedback from both the technicians and supervisors alike.
Bad Habit #11: Letting Planners Get Involved in Reactive Maintenance
The Planner is a very important position of any maintenance organization. Letting Planners step into reactive planning will sink any maintenance organization regardless of their resource capability. Planners must be allowed to be in front of the work, preferably for three to four weeks minimum. Planners’ duties include some aspect of master data and material master record management, so letting them firefight will be very destructive to equipment availability and the bottom line.
DATA
Bad Habit #12: Not Understanding the Importance of BOMs
Bill of Materials (BOM) is a key hand-off between two important business partners: supply chain and maintenance repair and operations. For the most part, organizations rarely understand who the process owner is. The bad habit here is far too often BOMs are overlooked not only by IT, but by the business as well. I have seen a number of Enterprise Resource Planning (ERP) implementations where the BOM aspect was overlooked entirely because of the sheer effort. Proactive methodology in equipment data management is critical to sustained growth of process. By employing effective BOM procedures, you enable your organization to focus forward, rather than react.
Core BOM data management affects every level of your value chain, including maintenance, procurement, engineering, production and materials management. We all know that the most critical part of maintenance processing is the detailed planning of our work. This practice, coupled with solid maintenance strategies over time, will eliminate 95 percent of reactive maintenance. This opens the door to world-class maintenance, safer work conditions and higher production yields. However, if BOM structure is poor and data management best practices aren’t in place, it won’t matter how solid the maintenance strategies; your planners are doomed to be reactive. If planners do not have effective BOM resources from which to draw from, they themselves will be reactive in the sense that they will spend most of their time fielding phone calls and chasing down pricing rather than walking down jobs in the field.
CONCLUSION
In establishing proactive maintenance, it is in imperative to focus on a few keystone habits. Keystone habits are changes that make success possible and will help to encourage other fruitful habits.1 These constructive habits unlock numerous other positive changes with far less effort than establishing a single habit from the ground up. If we look at it from a maintenance organization perspective, there are some keystone habits we can leverage to unlock an array of other positive behaviors:
- Hold meetings on time with solid cadence, complete with action items
- Provide feedback and enlist technician input on job planning
- Walk down all jobs
- Keep the shop clean
Often times, all the ingredients are in place for a proactive culture but we simply lack the change management skills to break the bad habits and take advantage of inflection points. An inflection point can be considered a turning point, after which a dramatic change, of which either a positive or negative results, is expected.1
To best recognize and take advantage of inflection points, I recommend the use of process coaches. Process coaches are individuals who have experience with both reactive and proactive maintenance organizations. Process coaches help facilitate the journey to a proactive maintenance organization. These individuals help your organization recognize inflection points and coach your team toward a proactive culture. Nothing is more effective in facilitating change than the experience of a peer talking your team through the change.
As leaders, it is imperative that we focus on good processes. We must also not lose sight of the engine that drives the process and the reason we are all here in the first place: our people. Developing your soft skills (people) by being able to identify these bad habits and act in a productive and respectful way has proven to be one of the most important elements in initiating a proactive maintenance culture. Maintenance proactivity leads to process sustainability and ultimately makes your team the masters of their own universe.
BIBLIOGRAPHY:
Topics: Article, Leadership
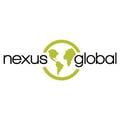
Posted by
Nexus Global
Recognized globally, across various industries, for delivering sustainable solutions that optimize both the organization’s assets and processes to yield a ROI of 10:1 or greater. Nexus Global Business Solutions, Inc. has been a worldwide leader in asset performance management and maintenance consulting, coaching and training for 15+ years.