Reassessing Preventive Maintenance Responsibilities Produces Savings
Part 2 of 2
The reallocation of responsibilities, the deletion of non-value-added PMs, the extended PM intervals, the deletion of duplicate PMs, and the implementation ofspecific value-added PMs were substantial changes. The results of the process were staggering. Among the more interesting results:
- Nine percent of all PMs were deleted
- Only 19 percent of existing PMs remained unchanged
- Nineteen percent of PMs added more details to a task
- The new tasks added represented 9 percent of total tasks, while another 9 percent of tasks were extended, meaning, for example, a PM task changed from weekly to monthly
The process also benefited the department’s use of labor. While the above results reflect a large reduction in non-value-added hours technicians had been spending performing PM tasks that seemed to do little or nothing in reducing the air compressor’s failures, the reality is quite the opposite. If you look at the failure history, the failures actually increased over a three-year period at a substantial cost.
During the workshop, the team identified PMs that had no impact on the compressor’s reliability, yet consumed many hours of the technicians’ capacity. As a result of the team’s efforts to reduce, delete, and extend PMs, an electrician who had spent 408 hours on PMs before the changes now spends only 168 hours, a reduction of 59 percent. A mechanical technician who had spent 816 hours now spends 662 hours, for a reduction of 19 percent, and an HVAC technician who had spent 1,263 hours now spends 942 hours, for a reduction of 25 percent.
The results also affected the department’s bottom line. Reducing the number of non-value-added PMs freed up maintenance hours that technicians used to perform more tasks that add direct value. Value-added utilization, or wrench time, rose from 22 percent to 38 percent, and value-added work hours per week rose from 8.8 to 15.2. With a total craft workforce of 50 technicians, an increase in available hours per week of 6.4, and an average hourly rate of $56.25, the annual cost reduction or avoidance was $936,000.
Downtime also improved as a result of the changes. The department realized significant financial benefits from performing the correct PMs on the air compressor and identifying potential failures. The team took a deep dive into the data to determine the historical failures of the compressor and the consequences of those failures. They then reviewed and modified tasks to identify that failure early. After topping out at $600,000 in 2014, downtime costs dropped below $100,000 in 2015.
Managers looking for opportunities to curtail costs can take this column as a prime example of the benefits of making the business case to perform an optimization workshop and review current PM strategies, all in an effort to reduce costs and increase asset performance and employee utilization.
Read Part 1 of 2
Topics: facilitiesnet, Article, Strategy Management
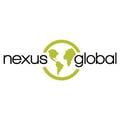
Posted by
Nexus Global
Recognized globally, across various industries, for delivering sustainable solutions that optimize both the organization’s assets and processes to yield a ROI of 10:1 or greater. Nexus Global Business Solutions, Inc. has been a worldwide leader in asset performance management and maintenance consulting, coaching and training for 15+ years.