Repair or Replace? Strategies to Keep Your Assets Afloat
Two years ago, I made a poor decision that cost me a boat. You see I made the decision to defer maintenance. I had plenty of time to do the maintenance, no worries. I was scheduled to be on the road for the next three weeks so when I got back, I would be sure to winterize the motor for the cold months coming. You can guess what happened next…
While I was gone, the weather took a wild swing where the average temperatures were well below normal. There was a stretch of 4 or 5 days where the temperature never got above 25 degrees. When I returned, my top priority was to do the maintenance on the boat. I started the engine up to run it for a few minutes and then continue with the required work. Something just didn’t sound right. I opened the bilge and water was spewing everywhere. Both manifolds were cracked beyond repair. You see water remained in the motor, froze, and cracked the manifolds. Expensive mistake, because I decided to defer the necessary maintenance in order to keep my asset functioning when called upon.
In the world of asset management, we ask questions about equipment and maintenance almost daily: Should we repair the equipment? Can we overhaul it? Can we just replace the unit altogether? How about deferring the work until next month? What factors determine the right path? The consequence of failure, the costs, and return on investment (ROI) are some of the key aspects managers need to consider in making the right decision.
Whether the issue is a boat or a main motor-drive, the issue of deferred maintenance comes up sooner or later. Wikipedia defines the issue this way, "Deferred maintenance is the practice of postponing maintenance activities, such as repairs, on both real property (i.e. infrastructure) and personal property (i.e. machinery) in order to save costs, meet budget, or realign available monies. The failure to perform needed repairs could lead to asset deterioration and ultimately asset damage. Generally, a policy of continued deferred maintenance leads to higher costs, asset failure, and in some cases, safety, health and environmental implications."
If a manager decides to defer needed repairs or replacement, what is the impact of continued failures? In some instances, there is the potential for environmental issues or violations. Safety and health also need to be considered. This includes service disruption, employee comfort, and other systems, as well. The criticality to the overall operation of this equipment has a significant impact on the decision-making process.
What costs should we consider?
It is important to realize that maintenance costs are only one part of the total costs we should consider. Best practice maintenance organizations consider the total cost of ownership (TCO) when evaluating options. Focusing exclusively on the direct cost will lead to less-than-optimal results.
In the case of motors, for example, direct costs include:
- Labor costs of removal and installation
- Materials costs for rebuilding, rewinding, or repairing
- Freight costs, which are commonly at a premium or expedited rate
But mangers also might consider the other costs:
- Efficiency loss
- Equipment downtime - costs of lost operator wages, utilities, etc.
- Customer service or comfort - hard to measure, but you sure do hear about it!
Repair or Replace?
Deciding if it’s time to repair or replace an asset can be difficult, but there are some questions to ask when making the decision.
How much will the repair cost?
When a pump motor fails, managers face a repair-or-replace decision. Many companies use a 50 or 60 percent rule for repairs or replacement. If a repair cost is more than 50-60 percent of the cost of a new motor, it is not repaired. If the horsepower (hp) of the motor is less than a certain threshold, the motor is scrapped and replaced. A company policy usually dictates this ratio. The cost and availability of replacement is also an important consideration when deciding whether to repair or replace.
How old is the asset?
If you’re considering when to replace an asset, use the average life span as a good reference point. The life span of an asset varies based on their usage and maintenance. What is the asset utilization requirements, 24/7 or a couple hours, weeks, or months? When considering an asset repair or replace, also note whether it is still under warranty and how many times you’ve run into trouble with it. I find it amazing how many organizations don’t have a formal warranty tracking policy in place.
Do we need to replace with a more energy-efficient equipment?
Energy costs are another important factor when deciding whether to repair or replace assets. If your equipment has a lower energy-efficiency rating than newer models, you might reduce costs in the long run by switching it out. Energy.gov is a great reference site with dozens of reports and white papers such as Determine Electric Motor Load & Efficiency.
Could better maintenance extend the life of the asset?
Most maintenance strategies were developed when the asset was new, and the original equipment manufacturer (OEM) recommendations were the basis for that strategy. Over the years, the strategy has been adjusted based on failures or performance. For instance, a lot of companies do a great job adding tasks to preventive maintenance (PMs), but a lousy job reviewing if that new task addresses a failure mode. That’s why I am a strong advocate for performing failure mode and effects analysis (FMEAs) or failure mode effects and criticality analysis (FEMCAs) on critical equipment. I recently completed a workshop conducting a formal FMECA on a crane. The outcome produced new strategies that addressed historical failures that were never previously addressed.
When managers must decide on whether to repair or replace a piece of equipment or entire unit, using lifecycle costing or a similar tool can assist in making the right business decisions. The decision they make will have profound impact on budgets, future operations, and the people in the facility. Remember, lowest cost is not always the lowest price. Don't wait until your operation is frozen before making a decision.
Topics: Article, Investigation Management, Strategy Management
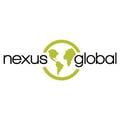
Posted by
Nexus Global
Recognized globally, across various industries, for delivering sustainable solutions that optimize both the organization’s assets and processes to yield a ROI of 10:1 or greater. Nexus Global Business Solutions, Inc. has been a worldwide leader in asset performance management and maintenance consulting, coaching and training for 15+ years.