Predicting Equipment Failures
Part 2 of 2
Adding It Up
What does all this math add up to? If managers do it properly, the calculations can determine when a piece of equipment might fail or the probability of when it will fail. With this information, managers can develop PM Optimization (PMO) strategies that will manage risk, improve preventive maintenance processes, introduce predictive maintenance technologies and ultimately reduce costs.
Managers who opt not to measure, track and respond to the results are putting their organizations at risk. It has been reported that reactive maintenance can be three-four times more expensive than proactive maintenance and that 30-33 percent of a department’s average maintenance budget is wasted on poor maintenance practices.
If equipment availability is lower than 95 percent, that could be a valid reason for a manager to conduct a formal root-cause analysis (RCA) or a failure-modes-and-effects (FMEA) analysis. Finally, in facilities with mission-critical equipment that must maintain a high level of availability and where the probability of failure is high, managers must take action to remedy the risk, such as redesigning or upgrading the component or the system.
When attempting to implement a reliability culture within a maintenance and engineering department, it actually will take managers some time to acclimate department staff and front-line technicians to a new way of performing and of thinking. It is considered common that when embarking on the reliability path, maintenance costs actually increase initially.
In Ron Moore’s book Making Common Sense Common Practice, he sights two studies.
The first study, Ormandy’s “Achieving the Optimum Maintenance and Asset Strategy and Ensuring They Are Aligned with Business Goals,” found that maintenance costs increased by 15 percent in departments making the transition to a reliability culture, but over time were reduced by 20 percent.
The second study, by C.D. Kelly, entitled “Leadership for Change: Developing a Reliability Improvement Strategy,” found the following results:
- Repair expenses increased by 30 percent during the first 12-18 months, then declined to 50-80 percent below the original levels after 24 months
- Breakdowns declined by 50-60 percent
- Downtime declined by 60-80 percent
- The spare parts inventory decreased by 20-30 percent
By measuring failure rates and probability of failure, the potential could be major dividends that help managers refocus their efforts to eliminate failure, unscheduled downtime and risk. Now if I could only use this data to help me bike faster.
Read Part 1 of 2
This content was originally published here.
Topics: Data Management, facilitiesnet, Article, Strategy Management
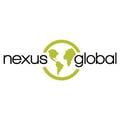
Posted by
Nexus Global
Recognized globally, across various industries, for delivering sustainable solutions that optimize both the organization’s assets and processes to yield a ROI of 10:1 or greater. Nexus Global Business Solutions, Inc. has been a worldwide leader in asset performance management and maintenance consulting, coaching and training for 15+ years.