Eliminate Physical Inventories, PERIOD!
Every year we must conduct an annual physical inventory. Corporate and finance mandate it. During those physical inventories, here’s what typically happens:
- Shut the warehouse operation down for the weekend or a couple days and freeze the transactions and inventory
- Call in warm bodies from the front office (HR, engineering, operations, etc.) for training on how to properly count
- Run the count tags and divvy up into count teams; one counter and the other a verifier
- Verify and record the count of the material
- Submit your count sheets and move to the next section but first, disappear for a couple hours
- Physical inventory completed, run variance reports
- Recount variance anything over $Xx
- Reconcile counts, post, and unfreeze inventory
- Spend the next 6 months correcting and fixing the miscounts from the warm bodies
Is this considered best practice? I argue, absolutely not! And the reason is because we cause more damage during a physical inventory than people realize. If you’re reading this, then you know what I’m saying. I’ve been audited more times than I liked to remember. I’ve facilitated or managed over 50 physical inventories in my career, not one of which was successful. Not because we weren’t prepared, but because we had people that didn’t know the inventory.
For example…
Individual versus box, ounces versus milliliters, gallons versus liters, yards versus meters, feet versus inches. Too lazy to open the box and count unopened packages. Just not wanting to be there and thus do a visual check. Everyone has gone through this before, but why?
Let’s get away from this antiquated practice and into world class. I had three policies in place when I managed warehouses around the world.
1. Cycle Counts
First off, there are three certainties in life…
- Death
- Taxes
- Cycle Counts-Random
Cycle counts must be random, not predefined. I’ve been to organizations that have a cycle count program, but they know the section they will be counting tomorrow. What’s the point? I know if my KPI is inventory accuracy and I know tomorrow I’m going to count this section; what do you think I’m going to do today???
We know that finance wants us to count 100% of our stock. That’s why we divvy up the SKUs into groups using A-B-C classifications. We count the As every quarter, the Bs twice a year, and the Cs once. Pretty simple concept. As represent the biggest risk while Cs are high volume/low cost items. When categorizing items into ABC classifications the standard percentage of value is:
- As = 15%
- Bs = 35%
- Cs = 50%
That’s how our cycle counts are setup. Keeping the math simple. We have a daily cycle count of 10 items; 2 of them are As, 3 are Bs and 5 are C class. This ensures we will count the entire inventory within the year.
2. Location Verifications
Not only did I have a daily cycle count, I also had the crew do what I called “Location Verification” cycle counts. What this means is that I don’t care what the counts are, I just want to know what’s in the location. Let me explain. Sometimes we get busy and don’t always document material movement. So, we receive an item and process it. The receipt transaction is done, but the material movement transaction is not.
My warehouse person moved it from the receiving dock to a location but didn’t do the transaction in the system. Or a technician comes into the storeroom, looks at the part (thinking they need it), but later changes their mind and places the item wherever is most convenient. I could go on about why parts are in the wrong location, but you get the idea and I’m sure you experience it. Location Verification was part of my cycle count program.
3. Quarterly Reviews
Third thing I did was conduct a quarterly review of the top 25 valued items in my inventory. Again, I’ve been audited more times than you can shake a stick at. I know what auditors look for and how they conduct an inventory audit. Every client that I work with, I do this exercise with a 60% success rate or 40% failure rate! I take the top 25 items in the inventory (either unit or extended costs) and conduct a physical review of each.
I look for the following:
- Is it there?
- Is the location in the system accurate?
- What condition is it in?
- Are there any missing components?
You would be amazed what the results are. As I said, I have a 60% success rate that the item is (1) found, (2) the condition is known, and (3) if any components have been bastardized off it.
I truly believe that if we have a robust cycle count program that is consistently executed, processes in place, and variances reviewed, you can comfortably eliminate yearly physical inventories and save yourself a lot of headaches by implementing some of these best practices into your daily activities.
Topics: Data Management, Work Management, Article
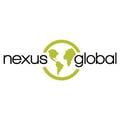
Posted by
Nexus Global
Recognized globally, across various industries, for delivering sustainable solutions that optimize both the organization’s assets and processes to yield a ROI of 10:1 or greater. Nexus Global Business Solutions, Inc. has been a worldwide leader in asset performance management and maintenance consulting, coaching and training for 15+ years.