Proactive Maintenance Supervisor
- Safety: Are hazards identified in advance and appropriately mitigated? Are safety protocols and procedures being followed? Are technicians wearing all required PPE?
- Job quality: Are the jobs being performed in accordance with precision maintenance principles and standards and in accordance with specs? Did the Work Order and Job Plan have the correct details the technicians needed?
- Job efficiency: Were there delays that impacted efficiency? How can those delays be prevented?
Today, many industries have elected to staff maintenance supervisory positions with supervisors who may have a background primarily in operations and production rather than maintenance. We recognize that this can present several challenges.
Lack of Technical Expertise:
Understanding of Equipment: Supervisors without a maintenance background may lack in-depth knowledge of machinery and equipment, which is crucial for diagnosing problems and understanding maintenance needs.
Technical Decision-Making: They might struggle with making informed decisions about repair techniques, preventive measures, and the selection of appropriate tools and parts.
Challenges in Safety and Compliance:
Regulatory Knowledge: Maintenance involves adherence to specific safety regulations and compliance standards. Supervisors without a maintenance background might not be as familiar with these regulations, potentially leading to compliance issues.
Risk Management: They may have less experience in assessing risks associated with maintenance tasks, increasing the potential for safety incidents.
Inefficient Resource Management:
Tool and Parts Knowledge: Supervisors may lack insight into the specific tools and parts required for various maintenance tasks, leading to inefficient resource allocation or delays.
Vendor Management: They may have less experience in managing relationships with suppliers or understanding the cost implications of different maintenance solutions.
Inadequate Troubleshooting Skills:
Problem Diagnosis: A background in operations might not provide the depth of troubleshooting skills needed for complex maintenance issues, leading to slower problem resolution and difficulties in assisting technicians who need help.
Decision-Making: They may rely more heavily on maintenance staff for technical decisions, potentially slowing down the decision-making process.
Training and Development Gaps:
Skill Development: Supervisors may not be as effective in training maintenance personnel due to a lack of technical expertise, which can impact the overall skill development of the team.
Knowledge Transfer: They may struggle to transfer knowledge and best practices related to maintenance processes effectively.
Communication Barriers:
Technical Communication: Effective communication with maintenance staff about technical issues, solutions, and procedures might be challenging if the supervisor lacks technical understanding.
Cross-Department Coordination: They might find it harder to coordinate maintenance activities with other departments, affecting overall operational efficiency.
It is common for combination production/maintenance supervisors to struggle to find time since often production issues may predominate and subtract time needed for maintenance supervision.
Although it may be a struggle, it is important to use time management skills to dedicate time for tasks such as:- Conducting safety briefings and pre-job briefings that apply to work scheduled for that week and that day and ensure coordination with other crafts/affected parties.
- Ensuring only valid break-in work and fill-in work are issued to the crew.
- Physically visiting job sites to observe safety, work in progress, and scheduling impacts.
- Addressing obstacles the technicians have in accomplishing work efficiently.
- Verifying post-maintenance testing and jobs are completed.
- Inspecting for job clean-up and ensuring the work site is returned to the original or better condition.
- Communicating with operations about the status and completion of jobs.
- Ensuring the return of unused materials to stores or staging areas.
Topics: Leadership, Maintenance, Proactive Maintenance
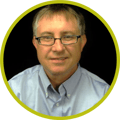
Posted by
Ken Arthur | CRL
Through his 30+ years of experience in various industrial industries, Ken is a global leader and expert in Work Management and Execution services. Ken delivers performance improvement in areas such as work management processes, leadership development, strategic planning, maintenance and process reliability, needs assessment, learning organization applications, and performance management and appraisal system design. Ken is also a veteran who served in the U.S. Navy.