Maintenance Planner Training... It’s Not Just for Planners
Maintenance Planning can be a challenging career choice. The job is often stressful with a never-ending stream of incoming work requests, a growing and disheveled backlog, competing priorities, a bureaucratic labyrinth of purchasing, and all the ins and outs of the CMMS. To get the necessary skills and knowledge, new planners need training not only in how to use a particular CMMS but also in Planning and Scheduling principles and practices.
However, training the planner/schedulers alone is not likely to allow an organization to realize true gains. Too many others significantly impact the Planning and Scheduling process playing vital roles in making and sustaining major improvements in backlog reduction, safety, wrench time, and reliability. The planner needs the collaboration and cooperation of many other people in both Maintenance and Operations. Training for Continuous Improvement of Planning and Scheduling is not just for planners, but for all those who affect and impact the process.
To begin with, planners are often misused and directed towards too many other duties that dilute the time they devote to their core function. They often wear too many hats, and the quality and effectiveness of planned work packs suffer. When management and supervisory staff in both Maintenance and Production are in training alongside planners, they are more easily aligned and can better implement, lead, and coach the Planning and Scheduling process. They speak the same language and have a common knowledge of fundamental principles and best practices in this essential organizational competency.
Training for maintenance team members should aim to equip the team to help improve Work Management with early problem notifications using:
- Quality Work Requests and Scoping
- Feedback on work package content, safety, work procedures, and methods
- QA/QC specifications
- Information documented in the CMMS for future job improvements
Good planning also aids reliability, and in this quest maintenance team members need to give feedback relative to failure modes, root causes, and procedural details requiring clarification or revision.
Production team members benefit when training gives the information they need to clarify their roles and responsibilities relative to their involvement within the maintenance Planning and Scheduling process. This includes:
- Equipment cleanliness standards to prevent defects from entering equipment
- Routine Operational Inspections
- Work Request System Specifications
- Coordinating and synchronizing production work with maintenance work using scheduling and communication protocols
Production team members’ impact is also greatly enhanced when given training on their specific equipment; how it functions, routine equipment care, inspections, troubleshooting, and One Point Lessons as well as other visual management tools necessary for knowledge sharing.
When a cross-functional multidisciplinary group from a plant hears the same training message and understands their roles and responsibilities for improving and sustaining Planning and Scheduling Excellence, the investment in training is maximized. The participants can establish a common understanding of Best Practices and how they transfer from the training classroom to the workplace. When Work Order feedback from the maintenance technicians includes what is needed from them with respect to safety, reliability, efficiency, and work quality, can harness the horsepower of the whole organization, which in turn accelerates the improvement of preventive and recurring corrective work packages across the board.
A fundamental roadmap to follow in your training approach involves:During the unfortunate occasions where planners are the sole participants in a training class, they always decry “The people who need to hear this aren’t here!” They are keenly aware of the impact managers and supervisors who didn't receive the training can have because they may not be aware of what the planners were taught and the support they need to be successful. Planners also complain they never get any feedback on the Work Orders, the priority system is misused, they have all kinds of problems coordinating with operations, etc.
Training maintenance and production stakeholders and aligning with planner training is a very effective approach for making rapid improvements in your Planning and Scheduling results.
Learn more about Nexus Global APM Solutions, AMP Software, and APM Training.
HAVE QUESTIONS? CONTACT US, WE'RE HERE TO HELP.
Topics: Work Management
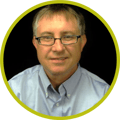
Posted by
Ken Arthur | CRL
Through his 30+ years of experience in various industrial industries, Ken is a global leader and expert in Work Management and Execution services. Ken delivers performance improvement in areas such as work management processes, leadership development, strategic planning, maintenance and process reliability, needs assessment, learning organization applications, and performance management and appraisal system design. Ken is also a veteran who served in the U.S. Navy.